Figure 1. RTO-LAB Platform
Within the i-STENTORE Project, UC3M is leading DEMO 3, which involves the integration of different storage assets into a distribution grid. UC3M is developing the integrated controls for real-time management, fed by the outcomes of an optimization package. The entire architecture of the demo could be tested in the RTO-LAB before the real implementation.
The RTO-LAB (Fig. 1) serves as an integrated platform for testing and validation of the various layers for the management and control of a grid in real time. The digital twin of the system, implemented in the real-time RTDS simulator, interacts with the power plant controllers (dSpace) and optimization packages (hosted in the industrial PC) via Modbus and Ethernet communication protocols. All devices are interconnected through the PLC in a system designed to allow multidirectional flow of information and control signals between all laboratory elements.
Fig. 2 demonstrates the performance of the integrated platform. It shows the power output of a power plant and a battery, along with their respective setpoints, which are calculated in real time every 5 minutes by an optimization algorithm hosted on the industrial PC. The PLC adapts and transmits the generated setpoints to the power plant in real time.
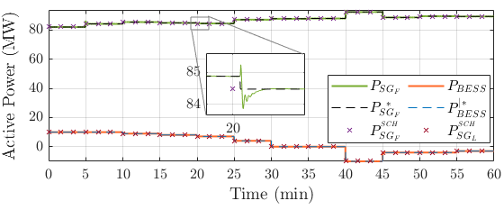
Figure 2. Scheduled power calculated by the real-time optimization, setpoint sent by the PLC and real-time power output of a power plant and a BESS including transient detail.